ISO 9001:2015: Making the Transition
- May 31, 2018
- Posted by: Kim Cunningham
- Category: ISO Tips
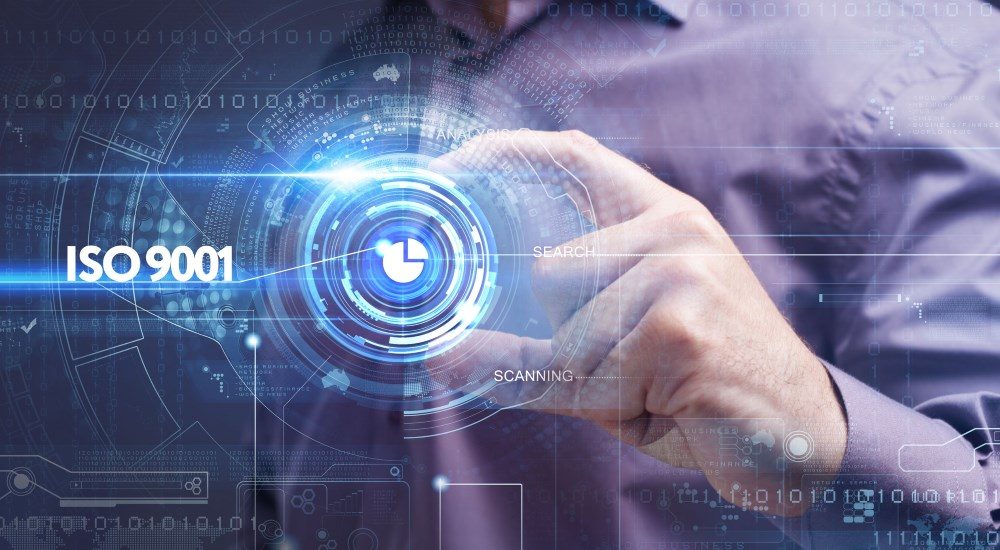
ISO 9001 is arguably one of the most influential standards available. Becoming certified in its quality management standards helps organizations to maintain efficient and consistent internal processes and gives customers confidence that they’ll always be receiving high-quality, reliable products and services.
However, the deadline to transition to ISO 9001:2015 is fast approaching. ISO 9001:2008 expires on September 14, 2018, which means that organizations have just three months left to complete the transition. If your organization hasn’t already made plans to transition before September, now is the time to start. This transition is important for a number of reasons. In this blog post, we’ll go through why you should transition and how to come up with a transition strategy.
For most organizations, the biggest reason to make the transition will be to avoid losing ISO certification. Organizations that don’t complete the transition by September will drop the certification, go into suspension, or have to get re-certified. Losing that certification can hurt your reliability with customers, some of whom look to ISO certification as a sign of sure quality. If your organization works with the government or other groups that require certification, you could stand to lose major contracts.
There are also internal benefits to your organization that should come from the new 9001 guidelines. ISO has revamped its quality management guidelines, with a focus on a more streamlined structure and more robust risk-management tools. The new version uses a common structure and simplified language, which will be especially useful to organizations that have multiple management systems in place. The 2015 version also has updates to leadership engagement and supply chain management. Going through the transition should therefore have some real benefits for your organization’s quality management.
If you are planning to transition, it’s essential to start now. The transition will require time, planning, and resources. The first step to take is to contact your local certification body and book a transition date. Their calendars will be filling up between now and September, so calling them as soon as possible is important. You should know that although ISO’s transition deadline is September 14th, some certification bodies may have an earlier deadline in place. Your certification body will likely also have their own transition guidelines that you can use.
The next step is fairly straightforward: read the ISO 9001:2015 standard. Guidelines from your certification body should help you to understand it – don’t be afraid to contact them with questions. You’ll need to identify changes in the new version that are relevant to your organization – these are the areas where you’ll need to update your quality management system.
Once you have an outline of the requirements you need to meet, it’s time to develop a plan. Some of the new requirements will require new work and solutions. For some of them, however, you may be able to use existing processes within your organization. Look to programs and processes that aren’t traditionally “quality control,” as these may meet the new ISO requirements. Using what you already have will help you to transition more efficiently.
The steps necessary to transition will be different for every organization. The key is to develop a plan, and leave yourself time to implement and review the changes before the September deadline.
If you’re feeling unprepared to complete the transition, look for a local workshop or consultants. Expert advice can help you to identify what changes you actually need to make and develop an efficient plan. That support may be key to completing the transition in the little time that’s left.
If your organization is already ISO certified, you don’t want to lose that certification and all the hard work that went into obtaining it in the first place. Transitioning to ISO 9001:2015 will require some work, but the good news is that there are guidelines and information in place to help you to do it.